ゴア® プライメア® (次世代型燃料電池向けMEA)ストーリー

執念で切り拓いた量産化の道
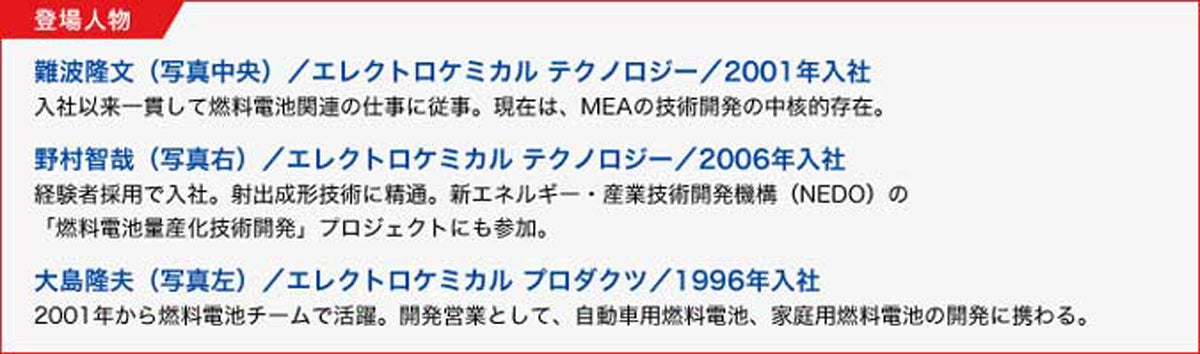
Chapter1 革新
技術の高さを証明したMESFA

2008年4月、燃料電池チームの大島隆夫(おおしまたかお)は、大手メーカーA社の本社を訪ねていた。バッグには、ようやく開発にメドがついた新製品のサンプルが、大事そうにしまわれていた。新製品は、燃料電池(※1)に用いられるMEA。日本では「膜/電極接合体」と訳される(※2)。燃料電池では、多くの場合、このMEAが数十~数百枚ほど積層されたスタック(※3)に酸素と水素が注入されて電気をつくる。いわばキーデバイスである。だが大島がサンプルで持参したのは、これまでのMEAとはまったく異質のものだった。日本ゴアがNEDO(新エネルギー・産業技術開発機構)のプロジェクトに参加し、3年の歳月を費やして開発に成功したばかりの新型MEA。社内では、従来製品と区別するために、これを「MESFA(メスファ)」(※4)と呼んでいた。
燃料電池は、21世紀の環境エネルギー分野におけるキーテクノロジーとして世界中で実用化に向けた研究が進んでいる。最も実用化が進んでいるのは、エネルギー効率が高く、環境にもやさしい「固体高分子形燃料電池」だ。ゴアでは、約20年前から固体高分子形燃料電池向け製品の研究に乗り出し、莫大な資金と人員を投じて製品開発を進め、ePTFEで補強したイオン交換膜「ゴア® ゴアセレクト® 」や、その表裏面に白金などの触媒層を形成しガス拡散層を一体化したMEA「ゴア® プライメア® 」を商品化。その技術力は、世界の産業界から注目を集めている。だが、これらの市場拡大を阻む最大の障害は、コストだ。日本政府は、燃料電池の劇的なコストダウンを促進する技術開発を民間に委託。その中で日本ゴアが3年がかりで開発に成功したのが、大量生産に適した新規MEAの「MESFA」である(※5)。

「MESFA」はその技術力を集大成して開発した最新の製品であり、他社に先駆ける次世代製品として社内の期待もかつてなく大きなものがある。固体高分子形燃料電池の製品化に取り組む家電メーカーや電池メーカーからも量産化に新たな道を切り拓く新技術として注目を集め、多くの引き合いが寄せられた。大島が担当するA社も、「MESFA」に強い関心を示したメーカーのうちの1社だ。大島は、はやる気持ちを抑えながらA社の正門をくぐった。
Chapter2 不安
解決の手段が見つからないままにスタートしたプロジェクト。
A社では、新型の燃料電池の開発が進んでいる。そのニューモデルに「MESFA」を使えば、今までのMEAと比べて3割程度コストダウンが可能になるというのが大島の提案だった。大島はサンプルを示しながら、燃料電池の商品開発を担当する技術者にアピールした。大幅な低価格化を実現して売れ行きに弾みをつけたいA社にとって、大島の提案は大いに魅力あるものに違いなかった。

ただ大島の中で、不安な思いもくすぶり続けていた。国の“お墨付き“があるとはいえ、実際の燃料電池に採用実績があるわけではない。また発売開始まで3年の時間的猶予があるとはいっても、少なくとも1年前に最終仕様を決定し、確認テストに入ることを考えると実質2年しかない。それまでにすべての仕様を決定し、品質をつくり込み、A社が求める量を製造する量産体制を確立できるのか。不安は、A社の担当技術者も同じだった。確かに「MESFA」は、コストダウンを考えた時、有効な手段には違いない。だが失敗を許されない燃料電池の商品開発にまだ実績のない新規デバイスを採用するのは、余りにも大きなリスクを背負うことにならないか。
最終的に、A社はそのリスクをあえて引き受ける決断をした。「MESFA」に寄せる期待が、それだけ大きかったといえる。大島がA社を担当するようになって、もうかれこれ7年。その間、燃料電池の商品化に向けて、熱い議論を交わしてきた。それだけに大島は、ともにチャレンジングなテーマに挑む決意を示してもらえたことが嬉しかった。「少し大変ですが、なんとか頑張りましょう」。大島は、担当技術者の言葉に背中を押されるようにして、決意と覚悟を新たにした。
Chapter3 立ちはだかる壁
ハイレベルなスペック要請、立ち入ることのできない「機密」の領域。

「MESFA」を市販製品に初めて適用する技術開発がスタートした。同じ燃料電池チームの二人の技術者、難波隆文(なんばたかふみ)と野村智哉(のむらともや)がプロジェクトに合流する。難波の役割は、顧客の求める仕様条件に応じたMEAの開発と、生産、品質管理など関係チームのとりまとめ。一方で野村は、MEAと樹脂フレームを一体化する成形法(生産プロセス)の開発を主に担当し、大島がA社と日本ゴアの間をつなぐパイプ役として様々な調整にあたる。

先方の技術者との間で、ミーティングが開かれた。顧客からMEAに必要とされる仕様その他の条件が示され、それをもとにサンプルを試作。次回ミーティングで最新の実験データや開発の現状を報告し、互いに議論しながら改善、改良を重ねていく。そんな繰り返しがしばらく続いた。万全を期して商品化したいという双方の思いから、打ち合わせは、しばしば6~7時間の長丁場となった。
特にMEAの開発で、難波を戸惑わせたのは「機密」という壁だった。A社の要求仕様に即してMEAを設計し、サンプルをつくって提示する。社内評価の段階では特に問題はないのだが、サンプルを使ってA社でスタックを組み立てると不具合が出てしまう。解決のためには原因を突き止める必要があるが、機密事項に触れるため、スタック化に関する工程については一切情報が明らかにされなかった。しかし、相手からの情報提供を待っていても、解決の糸口は見つからない。難波はあらゆる可能性を視野に入れてスタック化の製造プロセスを予測し、それを仮説として一つひとつ検証していった。野村をはじめチームのメンバーにも相談を持ちかけ、条件設定を変えながらテスト成形を繰り返して課題をクリアしていった。
Chapter4 跳躍
発想の転換とチームワーク。それぞれがもたらしたもの。

一方で野村は、樹脂フレームの成形法開発で悪戦苦闘を続けていた。A社から提示されたフレームの厚みは、1mmにも満たない。前職時代、射出成形部品の設計開発を担当していた野村には、到底達成できない数値に思えた。射出成形で加工が可能な厚みといえば、せいぜい2mm程度であることを知っていたからだ。だが、ここで引き下がるわけにはいかない。顧客の期待に応えることは、技術者の使命である。もしかすると、これは未知の領域の技術開発に挑むチャンスかもしれない。野村は自らの限界を越える気持ちで、成形機の圧力と、内部のMEAがダメージを受けない剛性との最適条件を探り続けた。社内のメンバーだけでなく、材料メーカーや射出機メーカーにも相談し、アドバイスを受けながら何度も何度も実験を繰り返し、厚みの壁を少しずつ突破していった。

プロジェクトの進展をよりスムーズなものにしたのは、チームワークだった。A社との定例の打ち合わせは、月1~2回ペースで開かれる。燃料電池チームの3人は、毎回欠かさず全員揃って参加した。いつもは東京と岡山にそれぞれ分かれて仕事をしているが、打ち合わせ当日は現地で合流し、昼過ぎにA社を訪ねるというのがなかば「ルール」になった。携帯電話が鳴り、画面に名前が表示されるだけで用件が分かるほど、日頃の連絡は密に取り合っていた。結束の強さは、燃料電池チームに限った話ではない。月1回開かれる社内の「マンスリーミーティング」では、「MESFA」開発について、製造や品質管理など関係メンバーから様々な意見やアドバイスが寄せられ、3人の話し合いの中で見つけられずにいた現状打開のヒントが、会議の中で見つかることもしばしばだった。当初野村が原因は装置にあると思い込んでいた歩留り改善のキーが、実はMEA製造プロセスそのものにあることが判明したのも、製造現場のメンバーとの意見交換の中でのことだった。そこかしこで自然発生的に話し合いの場が生まれ、活発に意見が飛び交う中で皆が気持ちをひとつにゴールに向かう――。“All in the same boat”、”Natural Leadership”。ゴアカルチャーは、このプロジェクトでも貫かれた。
Chapter5 誇り
新型燃料電池ついに搭載。成し遂げたものと、見えてきた課題。
紆余曲折を経ながら、スタートから2年後には本仕様も決まり、このまま進めば量産立ち上げは時間の問題と思われた。だがゴールを目前にして、プロジェクトは思わぬ危機に直面する。技術的な問題から、A社がいったん決まっていた仕様を再検討したいと話を切り出してきたのだ。すでに量産化に向けて材料の手配を終え、生産ラインも稼働まで秒読み段階での不測の事態だった。幸いMEAや一体成形に関しては開発していた技術の応用や調整でどうにか対応可能だったが、生産体制への影響は避けられない。3人は、関係チームとの調整に文字通り東奔西走しなければならなかった。それでも4ヶ月後に急遽仕様変更した「MESFA」をA社に出荷できたのは、以前にも増して全社一丸となった取り組みの結果だった。

燃料電池のニューモデルは、当初予定した期日通りにリリースされた。旧型に比べてサイズが大幅にコンパクト化されただけでなく、さらに価格も2割低減され、A社の技術者も十分納得のいく成果といえた。実際、新型の燃料電池は、想定を上回る出荷量をみせた。これは、エネルギー問題に対する認識が大きく変化しつつある社会情勢と無縁ではないと大島は言う。「我々が開発したMESFAをキーデバイスとする燃料電池が商品化されたことは、社会に非常に大きなインパクトを与えたと思います。政府や国民が、これからのエネルギー政策を考える際、代替電源のひとつとして燃料電池を選択できる状況をつくり出すことに貢献できたとすれば、これほど嬉しいことはありません」。
休みの日に、家族でショッピングを楽しんでいると、偶然自ら開発に携わった製品が陳列されたショールームに出くわしたことがあった。「お父さんがつくっているのはこれだよ」。二人の子どもに仕事を自慢できるのは、何よりもの喜びと大島は微笑む。

一方で難波は、燃料電池量産化の技術開発に一石を投じたことに意味があったとプロジェクトを振り返る。「燃料電池の普及に向けた技術開発は、これまでもっぱら研究開発に多くの時間が割かれ、量産化のための技術開発が議論される機会は極めて少なかったと思います。でもせっかく開発したエネルギー効率の高い優れた燃料電池を“絵に描いた餅”にしてしまわないためには、いかに量産化を実現するかが鍵を握っているのです。今回我々の取り組みは、燃料電池開発の最前線にいる多くの技術者に、量産技術開発の重要性を再認識させるキッカケになったと確信しています」
商品化が実現しても、MEAの技術開発が終わったわけではない。さらなるコストダウンに向けた取り組みに終わりはないと野村はいう。「量産は始まったものの、まだ改善の余地があるし、価格も爆発的な普及が望めるところまではいっていません。ハードルは高いですが、燃料電池チーム、さらには顧客の技術者の方達とも力を合わせてMEA量産技術を飛躍的にレベルアップし、燃料電池の普及につなげるのが今の目標です」。燃料電池チームは、早くも次の目標に照準を合わせている。
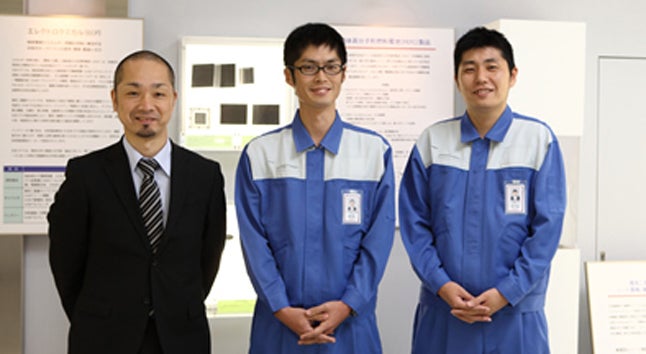
※1:燃料電池
電解質をはさんだ電極に酸素と水素を送り、化学反応で電気をつくり出すシステム。排出されるのが水だけで、CO2を一切出さないことから「究極のクリーンエネルギー」「21世紀の環境エネルギー分野におけるキーテクノロジー」と評される。また効率よく電気を取り出せるのも特色。ガソリンエンジンは最高でも40%程度しかエネルギーに変換できないが、燃料電池は水素の持つエネルギーの80%以上を電気エネルギーに変換できる。
※2:MEA(膜/電極接合体)
固体高分子電解質膜の両面に触媒層を形成し、ガス拡散層を一体化してつくる固体高分子形燃料電池の心臓部ともいうべき発電デバイス。このMEAに燃料ガス(酸素と水素)を供給すると、化学反応が起きて電気と水がつくられる。
※3:スタック
MEAを積層し、直接配属して高電圧を得られるようにした発電モジュール。「セルスタック」ともいう。
※4:MESFA (Membrane Electrode Seal Frame Assembly)
インサート成形と呼ばれる射出成形の技術を用いて、樹脂フレームをシームレスに一体成形したMEAの新品種。これによりMEAの剛性が飛躍的に向上。大量生産が可能となった。日本ゴアは、経済産業省の「燃料電池量産化技術開発」のプロジェクトに参加。3年の期間を費やして、2008年、技術開発に成功した。
※5:大量生産に適したMESFA
MEAは、何枚も重ね合わせた積層構造のスタックをつくる。そのため周囲のフチの部分に樹脂フィルムを圧着して補強している。しかし、このやり方だと加工に手間と時間がかかり、大量生産は難しい。そこで「MESFA」ではゴアの特殊樹脂加工の技術を用い、フィルムの代わりに樹脂フレームをMEAに一体化させている。このやり方だと加工に要する時間が数十秒しかかからないため大量生産が可能で、大幅なコストダウンが可能になる。